Prefabricating Poverty: The Political Implications of Prefabrication
ID
Reflections
Prefabrication’s promises are tempting: “lower and more predictable production costs, better and more standardized product quality, and faster and more punctual construction” (Noguchi, 2012, pp. 555–557) But, the real question is, tempting for whom? Let me pose this question in another way. Does the quote above, from The Encyclopedia of Housing (Carswell, 2012), mean to suggest that prefabricated construction results in greater numbers of affordable homes? Is it accurate to assume concerning prefabrication, as indeed, we have assumed about other “innovative” technologies historically, that it will help to improve living conditions for the general public? Moreover, who should contemplate these questions? Should the architect, as the individual who elects to employ prefabricated materials, be concerned about their material, as well as social and political, implications? And, should this issue and its implications be discussed among faculty and students at architecture schools in their courses of study? This brief article addresses these concerns in turn.
The concept of prefabrication is not new. Industrialized examples of its use are now more than a century old. So, why are the above questions more relevant now than ever? We can begin to address this question by studying the recent role of technological advancement in reintroducing prefabrication. Historically, prefabricated buildings were usually of lower quality compared to their on-site constructed counterparts. The reasons for this situation were rooted largely in manufacturing limitations. Consequently, large-scale prefabrication occurred during periods of workforce shortages. There are many examples of this phenomenon: new settlement houses in the British colonies in North America and Australia, the United Kingdom’s post-Second World War temporary houses (O’Neill and Organ, 2016) and the Soviet Union’s Khrushchyovka single-family public houses, built as alternatives to communal-style apartments from approximately 1960 until the dissolution of the Soviet Union in 1991.
However, the development of computer-aided manufacturing (CAM) in the past few decades has drastically changed the image and value of prefabrication, for both architects and the general public. For example, the complex façade systems of Frank Gehry’s Walt Disney Concert Hall in Los Angeles and Zaha Hadid’s Heydar Aliyev Center in Baku were almost completely prefabricated, but still praised by many for their design quality and aesthetic appeal. Thus, prefabrication is now being used not to overcome a temporary shortage in the workforce, but as a common strategy for building construction and, to some extent, even design.
David Harvey has argued that technology “has always been our great hope for resolving our difficulties” (2001, p. 62). This is definitely the case for prefabrication. Many architects and building construction professionals hope that lower construction costs resulting from widespread adoption of prefabrication will translate into increased access to affordable housing for individuals who otherwise might not be able to attain such shelter. I want here to ask whether this is a reasonable assumption. The U.S. Census Bureau’s housing affordability report provides at least a partial, and negative, answer to this concern (Wilson and Callis, 2013). Table 1 below, summarizes the general findings of that report and it vividly illustrates the downward trend in the percentage of American families and individuals that could afford to own a home in the United States between 1984 and 2009. Of course, housing affordability encompasses many more variables than the effects of prefabrication alone. Still, Table 1 suggests that this technology has not been functioning nearly as robustly to assist with affordability as its advocates have long hoped.
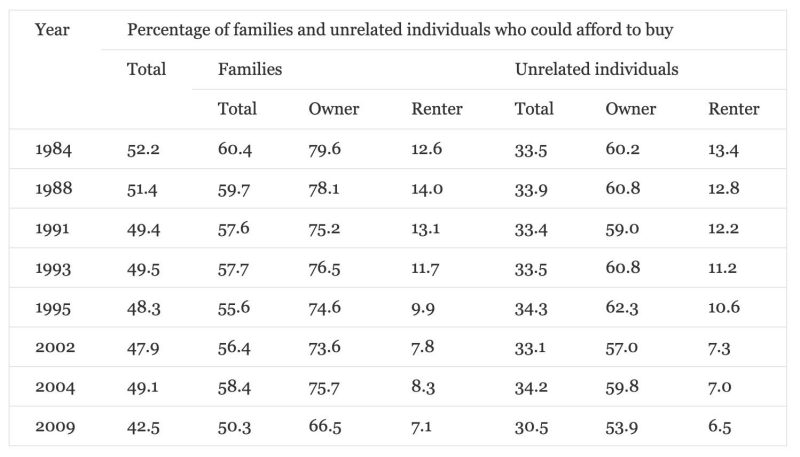
While prefabrication is not making housing more affordable for the general public, it is nevertheless having another large impact. To understand that implication of the technology’s widespread adoption, it is helpful to examine the issue through the lens of Marxist theory. Prefabrication is surely helping to lower the production costs of construction, in part by reducing the need for workers on the construction site. But this cost saving has not been translated into less costly homes, a fact that suggests that prefabrication has led instead to higher profits. Put differently, this shift in building construction technology has so far primarily resulted in increased income for manufacturers and construction companies. Nevertheless, and as an additional implication of this reality, “Capital accumulation has always been about speed-up” (2001, p. 123). By decreasing construction time, prefabrication can potentially accelerate the building process at different scales, which means not only that each building will be completed more quickly, but also that more projects may be undertaken simultaneously.
This reality implies that even as prefabrication has not improved housing affordability, it has diminished employment opportunities in the construction industry, especially for workers with lower levels of training. In this regard, it is important to remember that building construction has traditionally been an important source of jobs for vulnerable members of communities, including immigrants. A study of the impact of implementation of large scale prefabrication methods on the structure of the labor market in Hong Kong, for example, concluded that its widespread introduction could result in a 40% reduction in demand for construction labor (Tam, 2002). Perhaps predictably, the employment prospects of new immigrants from mainland China were the most adversely affected by this shift. This fact implies that, in the long run and intended or not, “The decision to promote prefabrication will become a political rather than a technical or managerial problem” (Tam, 2002, p. 402).
As one who has spent more than 10-years studying at different architecture schools in Iran and the United States, I think my experience of almost never discussing the political purport of my design choices with my instructors is typical. Moreover, the continued fragmentation of disciplines inside academic institutions limits the possibility of even (un)intentional encounters with this subject. Similar to many “new technologies,” prefabrication has always been treated as a positive characteristic in design schools even though its impacts for the general public are, in fact, uncertain and questionable, and its value to the architecture community may also be doubted except as a device to attract clients desiring to reduce the costs of construction. I find this scenario ethically problematic.
Finally, as Cross (2006, p. 7) and others have argued, defining and clarifying the problem at hand represents a fundamental part of design as an activity. In this case, that fact raises the question of how architects can realize a responsive design if they are ignoring key implications of aspects of the challenge at hand? Or perhaps put more generally, how can architecture schools prepare designers effectively while failing to address the political connotations of elements of their curricula? I believe that schools of design and construction are ethically obliged to encourage discussion among their faculty and students concerning the broader social and political implications of their professional choices.
________________
References
Cross, N. (2006). Designerly ways of knowing. London: Springer.
Harvey, D. (2001). Spaces of capital: towards a critical geography. Edinburgh: Edinburgh Univ. Press.
Noguchi, M. (2012). Prefabrication. In A. T. Carswell (Ed.), The Encyclopedia of Housing (2nd ed., Vol. 1, pp. 555–557). Thousand Oaks, CA: SAGE Publications, Inc. https://doi.org/10.4135/9781452218380.n191
O’Neill, D., & Organ, S. (2016). A literature review of the evolution of British prefabricated low-rise housing. Structural Survey, 34(2), 191–214. https://doi.org/10.1108/SS-08-2015-0037
Tam, C. M. (2002). Impact on structure of labour market resulting from large-scale implementation of prefabrication. In Advances in Building Technology (pp. 399–403). Oxford: Elsevier. https://doi.org/10.1016/B978-008044100-9/50052-8
Wilson, E., & Callis, R. R. (2013). Who Could Afford to Buy a Home in 2009? Affordability of Buying a Home in the United States (No. H121/13-02). U.S. Census Bureau. Retrieved from https://www.census.gov/library/publications/2013/demo/h121_13-02.html
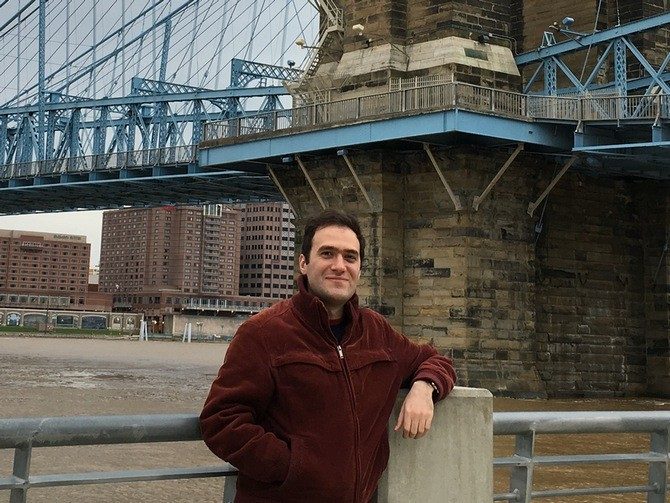
Reza Fateminasab is a PhD student in the Architecture and Design Research program in the School of Architecture + Design at Virginia Tech. He received his Master’s degree from the University of Tehran and his Bachelor’s degree from Tehran University of Art, both in architecture. His current research focuses on the design process and implementation of digital tools within it. He enthusiastically follows the arts and politics.
Publication Date
March 29, 2018